Full article may be viewed here. Credits to…Kristina García – Writer & Eric Sucar – Photographer.
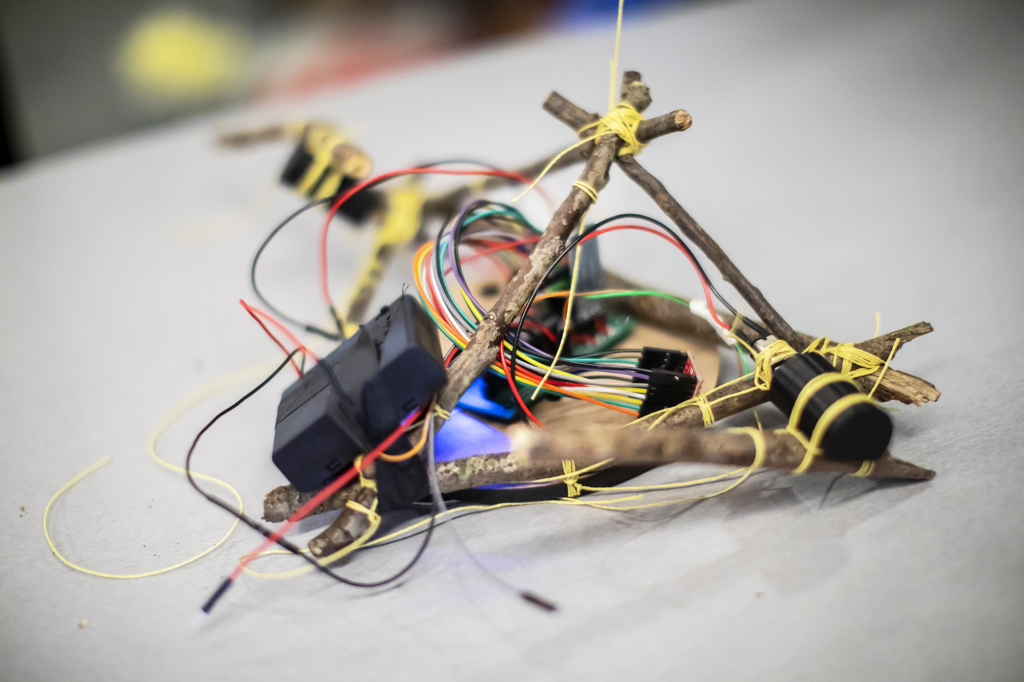
In late summer, just as the leaves were starting to crisp and curl in the heat, Devin Carroll walked out of his apartment, looked on the ground, and picked up a couple of sticks that he thought might work for his robot. About half an inch thick and the length of an adult hand, he stripped the three sticks of their bark and lashed them with string to StickBot, a modular robot composed of circuitry, actuators, a microcontroller, and a motor driver.
Powered by four AA batteries, connected by a maze of wires and blinking lights, StickBot’s wooden arms now thump up and over, powering the robot across the table at Penn’s General Robotics, Automation, Sensing & Perception (GRASP) Lab, where Carroll is a Ph.D. candidate in the School of Engineering and Applied Sciences.
Controlling the robot using an app he designed, Carroll shows how StickBot can pivot from using the sticks as legs in “crawler mode,” to using them as arms. In “grasper mode,” the sticks are attached to a controller plate on one side to form a hinge joint while moving with their free end to hold a cup upright.
Rather than a static, singular invention, StickBot is an idea, a flexible system that can be reconfigured in a variety of ways. A modular robot, StickBot’s components can be added, adjusted, and discarded as needed.
Mark Yim, Carroll’s advisor, has been at Penn for 17 years and is the current director of the GRASP Lab. The high versatility of modular robots presents a lot of potential for the technology to evolve, Yim says. One iteration of this is self-configuring robots. “People are really good at adapting to different environments: When it gets cold, you put a coat on. And robots can do that as well. But if robots could also change their shape, do different things … it gives you more possibilities.”
In addition to a robot made from sticks, Carroll has also built a robot made from ice. With a rectangular body and two large wheels, the robot looks like a cross between a monster truck and a Cushman cart. It’s called, of course, IceBot.
IceBot landed a 2020 entry in the Guinness Book of World Records as the first robot made entirely out of ice (save its motor driver and actuators, which Carroll embedded into carved holes). Carroll hopes this technology will be used one day to carry out missions in Antarctica or on an icy moon, possibly as a self-configuring robot. For now, it is a way to refine his ideas about modular robots.
“The lesson learned from IceBot,” Carroll says, “is, don’t be afraid to try a crazy thing. It might just work.”
Found objects, reusing materials
With StickBot, Carroll continued his creative experimentation. This time, he focused on keeping the costs low and creating a simple system that could perform an array of tasks.
“StickBot is a robotic system that is intended to provide users with a large amount of flexibility at an extremely low cost and we do that by leveraging the modularity of found materials,” says Carroll. “We have a bunch of tree branches or sticks and we’re able to assemble them into truss structures in different configurations. In doing so, we can get things like a crawler robot or a gripper robot or really, anything you can imagine. Behind StickBot is the ability to reconfigure things and to make it extremely affordable.”
Carroll estimates that StickBot’s total build cost is under a hundred dollars for a simple model, although larger systems may cost more. While some components (like the actuators and motor driver) are integral to the robot’s function, others can be swapped out depending on the task being performed and the materials at hand. (Carroll is exploring the use of hot glue and duct tape in lieu of string.) The robot should be able to be constructed from things people might have on hand, he says.
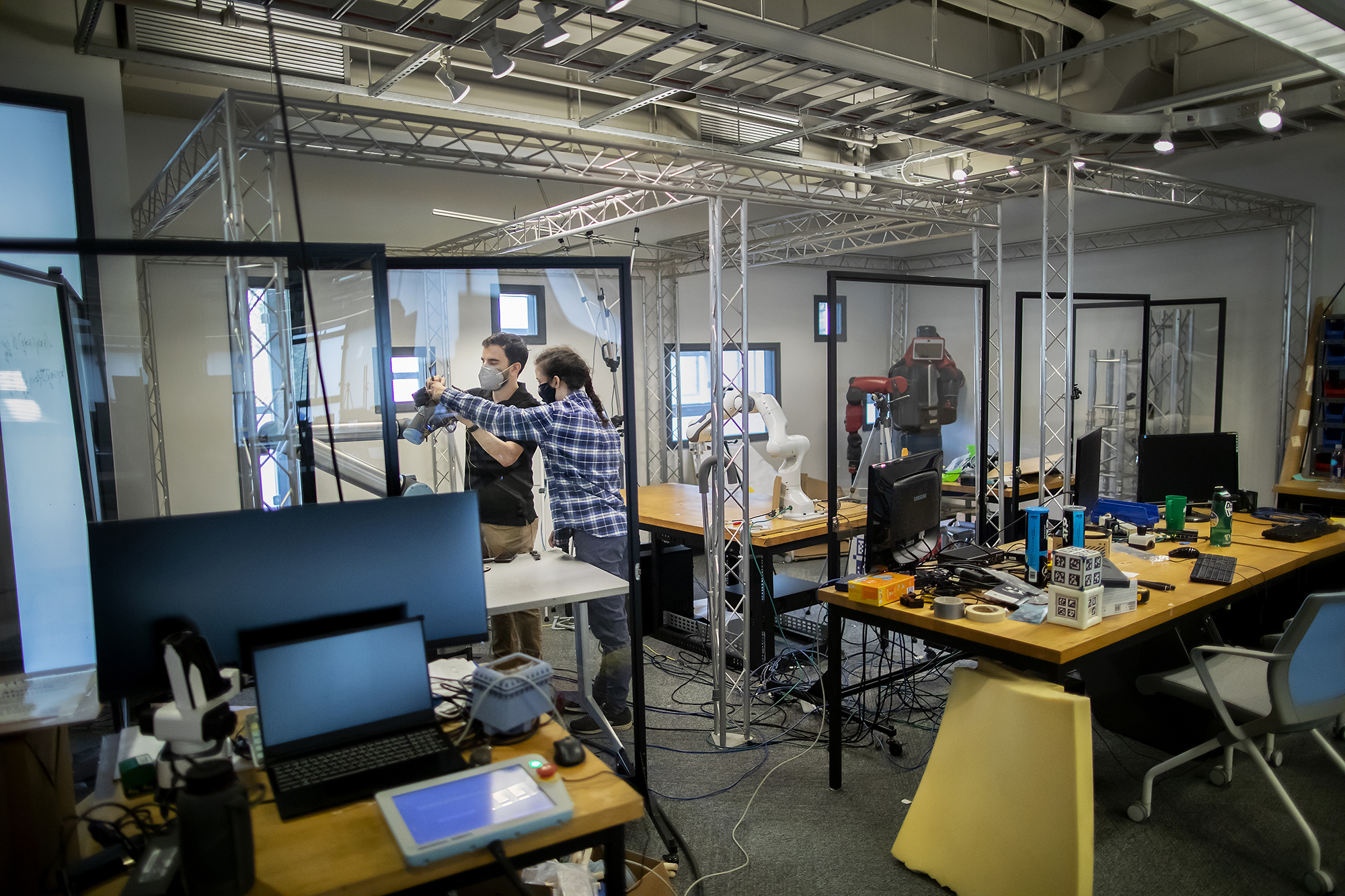
The reduce, reuse, and recycle ethos has been with Carroll since he was young. Carroll grew up on a farm in rural Massachusetts. He was a member of 4-H; he raised sheep. “Everything we did was intended to be renewable,” Carroll says. “Building things like barns or sheds, we would try and reuse as much material as possible.”
Later, Carroll went to the University of Massachusetts Amherst for mechanical engineering and did a summer Research Experience for Undergraduates (REU) program at Harvard, where he built his first robot. “I was a sophomore in engineering school, had no clue what I wanted to do,” Carroll says. “I had been working that winter at Harvard Forest, just doing maintenance for them. A researcher came up to me and said, ‘You’re a mechanical engineer, right?’ Can you build this robot for me?”
Carroll built the robot, “essentially a box with a bunch of sensors,” he says, and designed a tram runway in the tree canopy, three scaffolding-heights high. Powered by a solar-charging battery, the robot was designed to traverse an area to help ecologists determine how quickly the forest would regrow following a clearcut.
It was an influential experience for a young engineer. “There I was, surrounded by ecology and trees and all of those researchers and scientists. People there were very focused on how we can affect the world around us in a positive manner and create a renewable resource so we’re not just using something up, we’re actually giving back.”
Affordable and accessible
One possible application for a StickBot-style robot is rehabilitation settings in global health care, either as a prosthetic or in therapy. High-end medical procedures are all well and good, Carroll says, but are they affordable in every setting? And once that high-tech device breaks, how easily can it be fixed?
“If we could deploy the robotic system like StickBot in a scenario such as that, suddenly we can make an impact in the lives of many more people,” says Carroll. Because StickBot is a relatively simple modular robot, its components can more easily be repaired and replaced.
“By providing people with the ability to use materials around them, we do two things,” Carroll says. “One, we cut the cost of materials, which are marked up. Two, we can reduce the complexity without reducing the operational function.”
It’s definitely a timely idea for global health, says Michelle J. Johnson, associate professor of physical medicine and rehabilitation in Penn’s Perelman School of Medicine. Johnson, who is director of the rehab robotics lab (A GRASP Lab), also does research in Botswana. “One of the big issues is affordability,” she says. There is a need to support clinicians in lower resourced settings, but how do we do that?”
The concept of affordable robots that leverage material that is local and plentiful is compelling, Johnson says, because when materials and electronics have to be imported, costs can increase rapidly.
A modular robot can also be customizable and health clinics could invest in the robot’s functionality over time. “Maybe today you can afford just one module, and then tomorrow you can afford the second, and now, you have a system you can use in multiple ways,” Johnson says. “You can build as you go.”
The StickBot system has potential to be used as a social, therapy, prosthetic, or assistive robot, Johnson says. In Botswana, some of Johnson’s patients have HIV, which can trigger strokes. A therapeutic robot like StickBot could be used to support an immediate functional need or help patients to perform a physical therapy exercise, she says.
The functional application of ideas is important to Carroll. He wants everyone to have access to interesting design that has the potential to improve lives.
“Have you seen ‘Big Hero 6’?” Carroll asks. He thinks the Disney movie should be required viewing, at least for those interested in robotics. In it, the hero attends an engineering presentation for students and holds up his invention—something that looks like a tiny iron filing, smaller than a pinky finger. The audience is not impressed. Then, the hero shows what thousands of these little doohickeys can do. The modular robots link together and break apart again, effortlessly building scaffolding, and creating an upside-down moving walkway. The possibilities are only limited by the hero’s imagination.
“Having the flexibility to do more things means that you can help more people,” Carroll says. “And if you can make it inexpensive, that’s even better.”
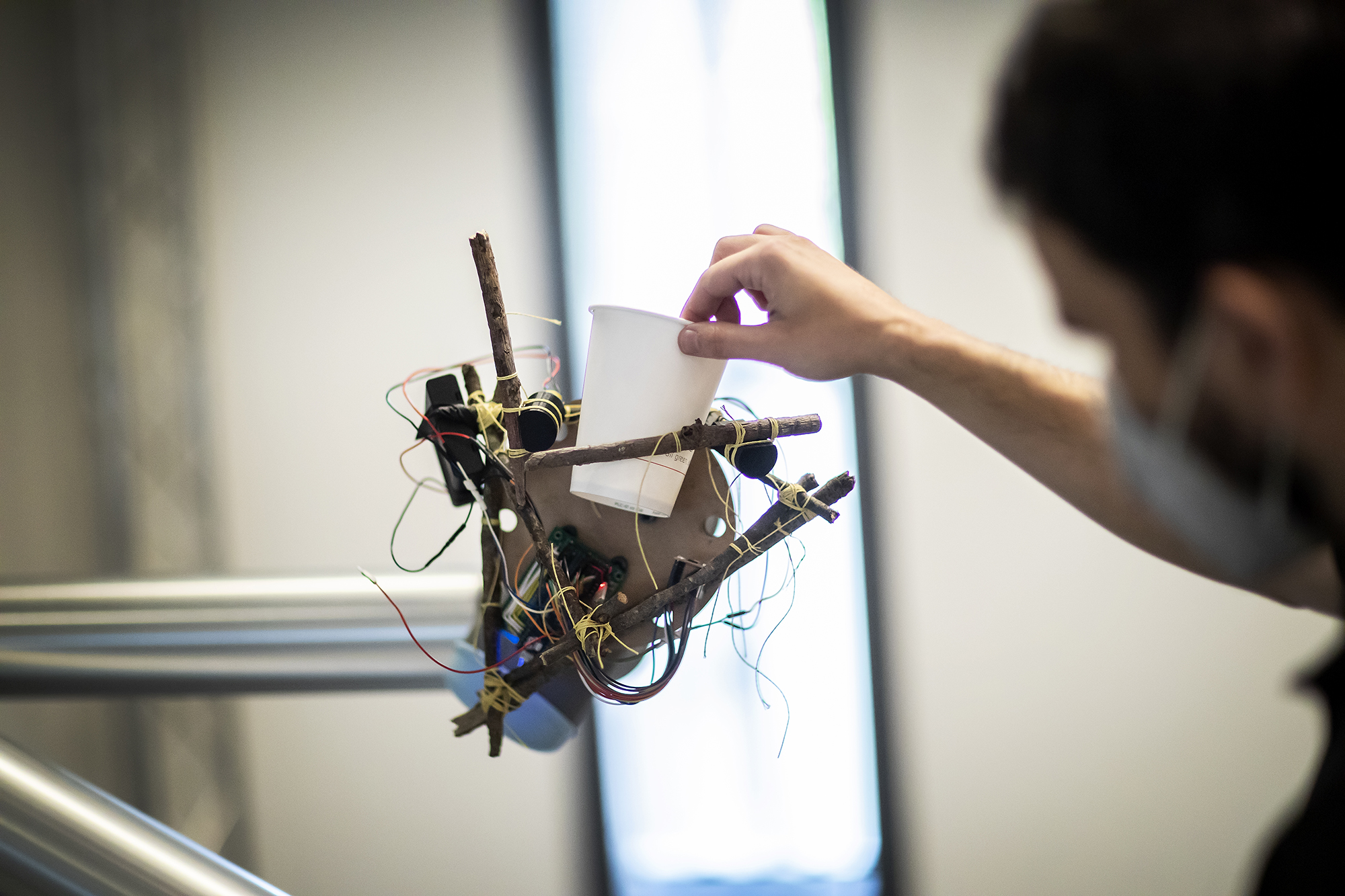